
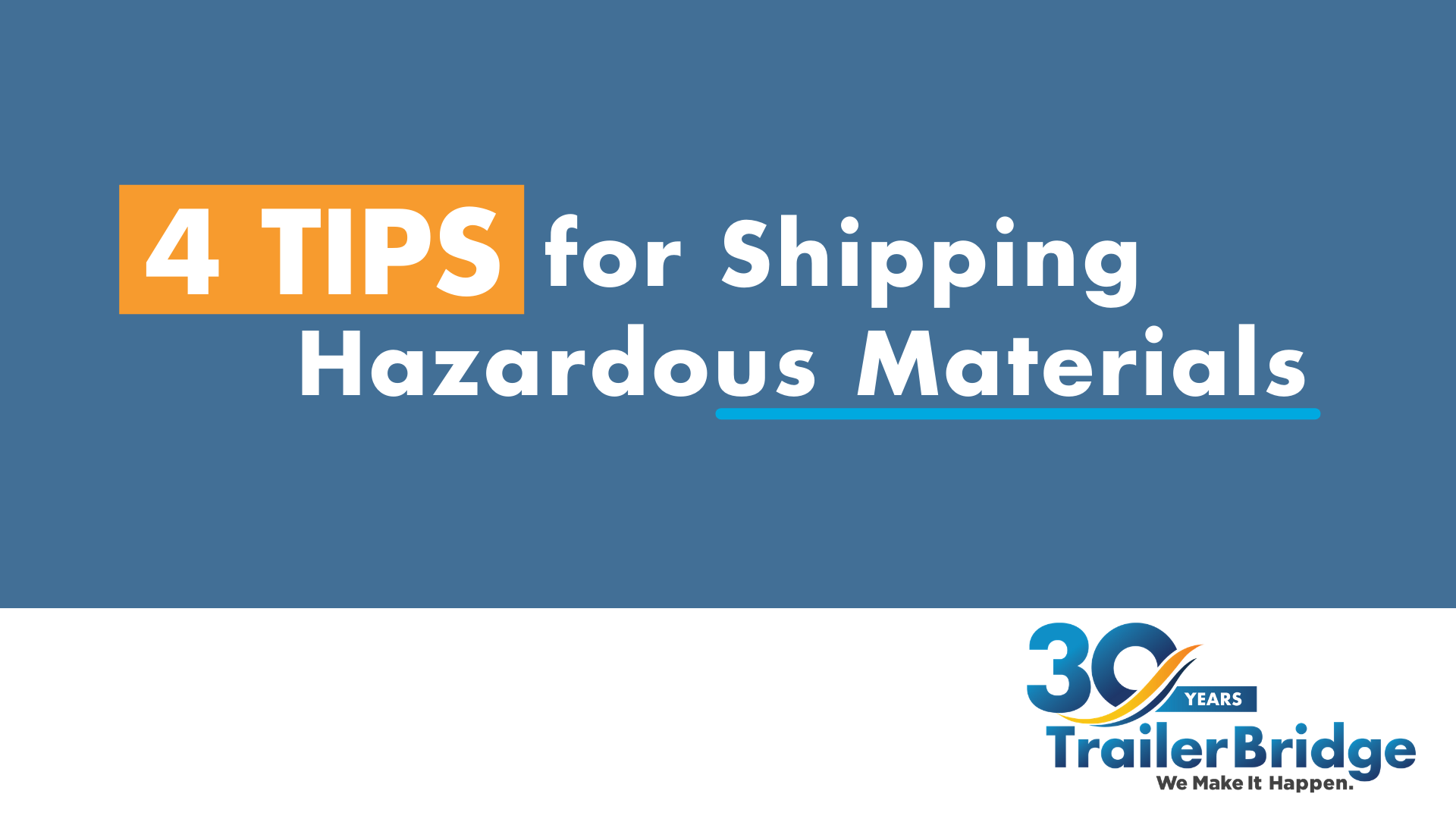
4 Tips for Shipping Hazardous Materials
Shipping hazardous materials can be complicated and it can be surprising how many common consumer products are classified as dangerous.
The US Department of Transportation (DOT) requires companies to train and certify employees in handling and processing dangerous goods. The regulations are so important that companies who willfully ignore the rules will be fined for non-compliance and may encounter legal action.
Trailer Bridge handles many hazmat inquiries per week and is equipped to be your trusted partner for shipping this sensitive cargo. In this blog post, we’ll discuss four important considerations for shipping hazardous materials: compatibility, segregation, placards, and documentation.
Compatibility: hazardous materials and their shipping rules
Hazardous materials are divided into nine classes based on whether they are explosive, gases, flammable, poisonous, infectious, radioactive, corrosive, or otherwise dangerous. Each category of hazardous material comes with specific shipping and packing instructions, as well as a permitted shipping quantity.
Some hazardous materials are obvious. Gasoline, propane tanks, and fireworks are good examples. However, it can be difficult to know which everyday products are hazmat. Batteries, airbag inflators, fire extinguishers, oil-based paints, and nail polish are just a few ordinary items categorized as dangerous during transport. How would you ship some of these products?
Any hazardous product will have a safety data sheet (SDS) provided by the manufacturer. The SDS should be provided to shippers and handlers and contains 16 sections covering an item’s general properties, hazards, protective measures, and safety precautions when handling it.
The International Maritime Dangerous Goods (IMDG) Code regulates the shipment of goods by sea. Before we ship hazmat products together, we check each substance in our in-house IMDG code database. For example, if a shipper wants to move batteries wet (filled with acid) alongside polyamines, we would investigate their UN numbers and see that these can’t be shipped together.
Where items can be shipped together, the system tells us exactly what packaging requirements exist, whether the products are compatible, if they need to be segregated, and what placards are required.
Segregation: approved packaging and shipping containers
Hazardous materials handling is governed in general by Title 49 of the Code of Federal Regulations. Each kind of hazardous material requires approved packaging and containers. For example, a liquid product might need to be shipped in steel drums rather than aluminum or plastic.
Shippers should consult the packaging section of the DOT’s Hazardous Materials Table to find out the correct hazard class. This will determine whether a product needs single, composite, or combination (inner and outer containers), or performance packaging. Shippers should consult a product’s safety data sheet, which will list its “packing group.”
Suppliers like chemical manufacturers, auto parts stores, industrial distributors may be shipping many types of hazardous materials in limited quantities, but special precautions must be taken when any one item exceeds 1,000 lbs.
Markings, labels, and placards
How your product is marked and labeled depends on its hazard class, ID number, weight, and other factors.
Markings are attached to outside packaging and include information like a descriptive name, ID number, instructions, cautions, weight, specifications, and UN marks. Examples of markings are arrows indicating the package orientation, directions to keep it away from heat, and a statement that it contains Lithium batteries. There are special markings for radioactive, poisonous, and limited quantities.
Warning labels are placed near the markings on containers. Labels identify hazards in the product and use colors, codes, and pictograms. They are diamond-shaped and identify which of the nine classes of hazardous materials the product belongs to. Warning labels need to be at least 3.9 inches on all sides.
Placards are very similar in design to warning labels, but need to be at least 9.84 inches on all sides. Placards are placed on all four sides of transport vehicles or bulk packaging.
On the road: shipping papers and driver’s license endorsements
You may need to provide additional paperwork to logistics companies when shipping dangerous goods. The general description of the goods will include information like the UN ID number, ID number and proper shipping name from the DOT Hazardous Materials Table, hazard class, packing group, quantity, number and type of packages, emergency contact information, and shipper’s certification.
When hazmat moves over roads, drivers must have an H endorsement (hazardous material) on their driver’s license. This requires a background check by the Department of Homeland Security every time they renew their license. By law, drivers should receive training every three years, but here at Trailer Bridge, we do this training every two years.
Get started with hazmat shipping
Shipping hazardous materials is a multi-step process that requires planning and strict compliance. Do your research ahead of time to ensure you understand what your specific products require in terms of packaging, labeling, and shipping.
We at Trailer Bridge are here to help you learn more about your specific hazmat shipping needs. Contact us today to get the conversation started.